Carbon accounting 101 for logistics managers
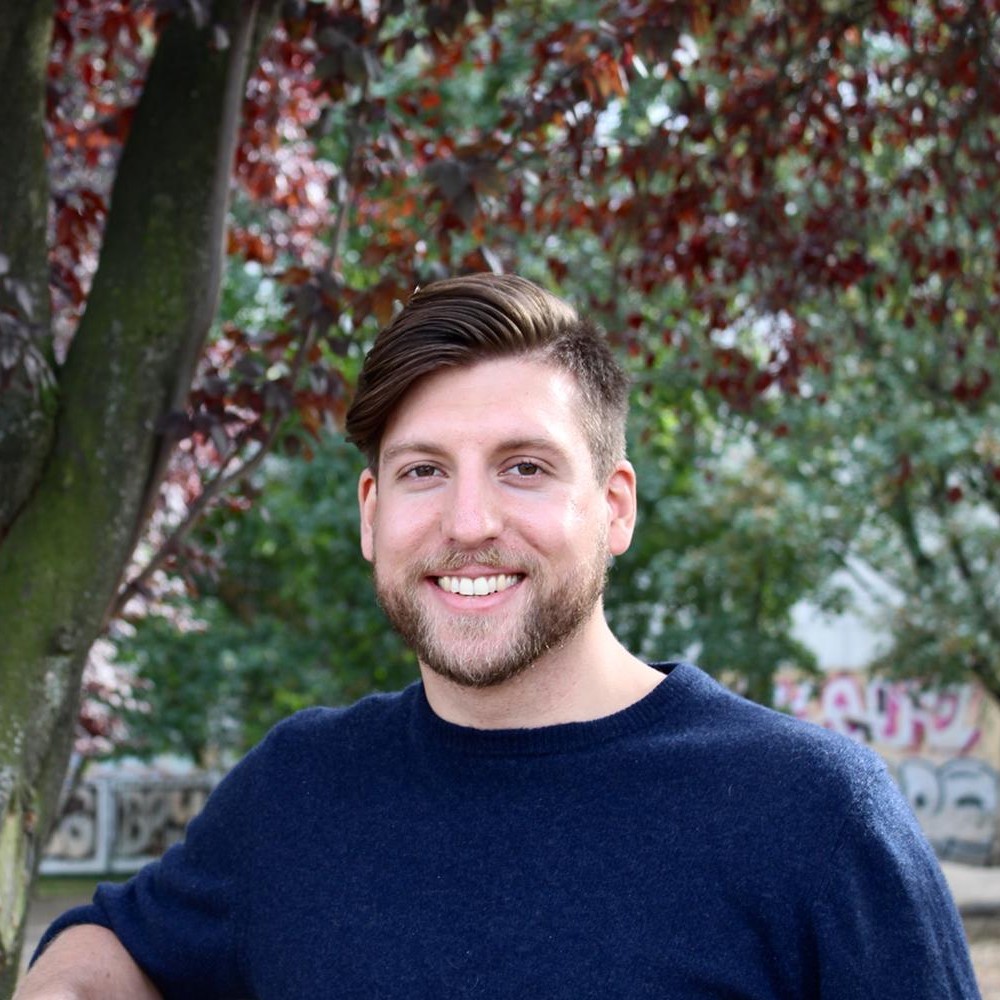
Greg Herz, Content Lead
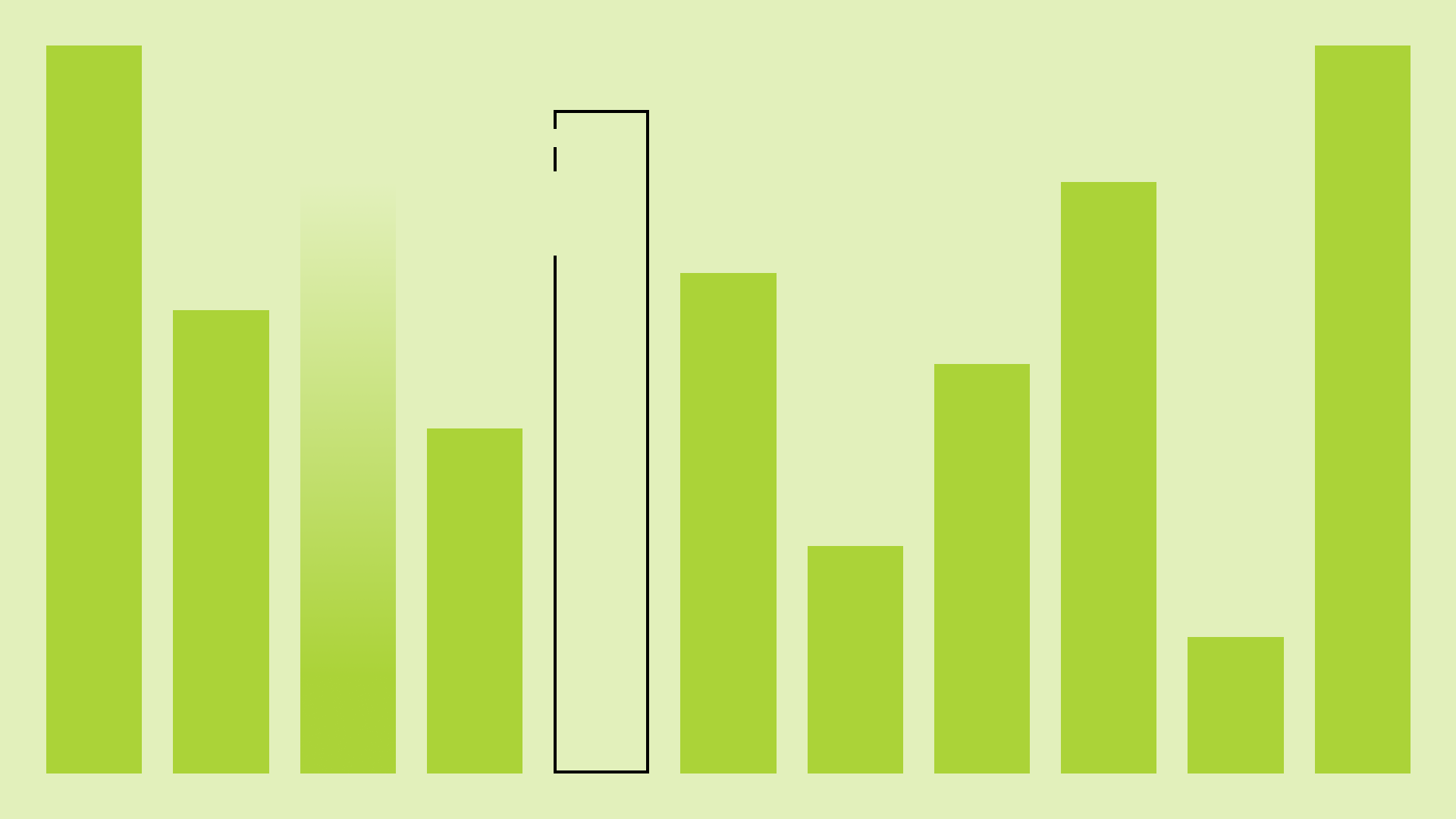
Carbon accounting can be complex, but it should also be a crucial part of every business's procurement process in the modern era. As the need to become more sustainable gathers momentum, understanding your company's carbon footprint is no longer a nice to have — it should form a core part of your business strategy.
In this blog post, we’ll provide you with an introduction to carbon accounting tailored specifically for logistics managers. You’ll learn about the fundamentals, including what carbon accounting is, why it matters and how it’s done. We’ll dive into how you actually do carbon accounting — from calculating emissions right through to the reporting process, and we’ll also offer solutions that make it more manageable for you, your team and your logistics providers.
With this knowledge, you will be able to comply with emerging regulations and position your company as a leader in sustainability — a crucial competitive advantage in today’s market.
Section 1: The basics of carbon accounting
What is carbon accounting?
Carbon accounting is the checks and balances of a business’s contribution to climate change. As businesses become more aware of their responsibility to manage and reduce their carbon footprint, carbon accounting has become vital for measuring and managing their greenhouse gas (GHG) emissions. With the data and insights collected during the carbon accounting process, businesses can go on to identify reduction strategies, enhance their sustainability credentials and meet climate disclosure regulations.
A good way to think of carbon accounting is to compare it to financial accounting. In the same way that financial accounting tracks a business’s income and expenses to assess its financial health, carbon accounting logs all of its GHG emissions to evaluate its environmental impact.
Carbon accounting is an essential practice in the global effort towards net zero. It can help you understand your business’s environmental impact, identify cost-saving opportunities and enable you to position your business as a sustainability leader.
What are GHG emissions?
Greenhouse gas emissions, or GHGs, are gases that trap heat in the Earth’s atmosphere. This causes a warming effect called global warming which will eventually make the Earth inhabitable for humans.
Here’s a run-down of the main greenhouse gases and their major sources:
Carbon dioxide (CO2): Burning fossil fuels, deforestation and industrial processes.
Methane (CH4): Livestock digestion, landfills and fossil fuel extraction.
Nitrous oxide (N2O): Agricultural fertilisers, industrial activities and burning fossil fuels.
Hydrofluorocarbons (HFCs): Refrigerants, air conditioning and aerosol propellants.
Perfluorocarbons (PFCs): Aluminum production and electronics manufacturing.
Sulfur hexafluoride (SF₆): Electrical insulation and circuit breakers.
Nitrogen trifluoride (NF₃): Semiconductor manufacturing and flat-panel display production.
Due to their differing lifetimes (the time a GHG particle remains in the atmosphere) and differing energy absorption potentials, some GHGs have a greater impact on the environment than others. This can make quantifying a business’s total GHG estimate — otherwise termed “carbon footprint” — a challenge.
What is a carbon footprint and how is it calculated?
A carbon footprint is the total amount of GHGs emitted both directly or indirectly by a person, organisation or product. It can be thought of as a measure of the environmental consequences of our activities.
For your business, the carbon footprint represents the total net GHGs released as a result of your operations. This includes emissions from your own activities, such as energy consumption, transportation and waste disposal, as well as emissions associated with the production of goods and services you use.
Although it refers directly to carbon, a carbon footprint encompasses the total amount of all GHGs, and is quantified by converting their impact into a single unit of measure called a carbon dioxide equivalent (CO2e).
What is CO2e?
While CO2 is a specific GHG that is naturally present in the atmosphere, CO2e is a standardised unit for measuring the total impact of all GHGs in terms of the amount of CO2 that would have the equivalent environmental impact.
To calculate the CO2e of a specific amount of a GHG, you need to know its Global Warming Potential (GWP), which is a measure of how much heat a specific GHG traps in the atmosphere in comparison to CO2 over a specific period (usually 100 years).
How do you calculate CO2e?
To calculate a GHG’s CO2e, you use this formula:
CO2e = Amount of a particular GHG x Its GWP
Here’s an example of how 0.5 tonnes of methane, which has a GWP of 28, would be converted into CO2e:
0.5 (amount of methane produced in tonnes) x 28 (methane’s GWP) = 14 tonnes CO2e
To calculate your business’s total carbon footprint in CO2e, you need to use this formula to convert the total amount of each GHG produced by its operations into CO2e, and then add these together.
As some GHGs have extremely high GWPs, such as some HFCs and SF6 (which can be in the tens of thousands), even a small amount can have a considerable impact on your business’s overall carbon footprint. A full list of GHGs and their related GWPs can be found on the Greenhouse Gas Protocol’s Global Warming Potential Values factsheet.
Understanding sources of carbon emissions in your business
What are scope 1, 2 and 3 emissions?
Defined by the Greenhouse Gas Protocol (GHG Protocol), a business’s emissions can be broken down into 3 emissions types, or “scopes”, which can be categorised as direct or indirect GHG emissions associated with a company’s operations. Here’s a breakdown of how the 3 emissions scopes are defined with working examples:
Scope 1: These are direct emissions produced from sources owned or controlled by the company.
Example: Fuel combustion in company vehicles or within manufacturing plants.
Scope 2: This encompasses indirect emissions from energy.
Example: Emissions from electricity, steam, heating and cooling that a company purchases and uses, although not produced directly by the company itself.
Scope 3: All other emissions (outside of scopes 1 and 2) that occur in a company’s value chain, such as those emitted by suppliers and throughout end-to-end product lifecycle.
Example: Emissions produced by suppliers delivering parts to a company’s factories.
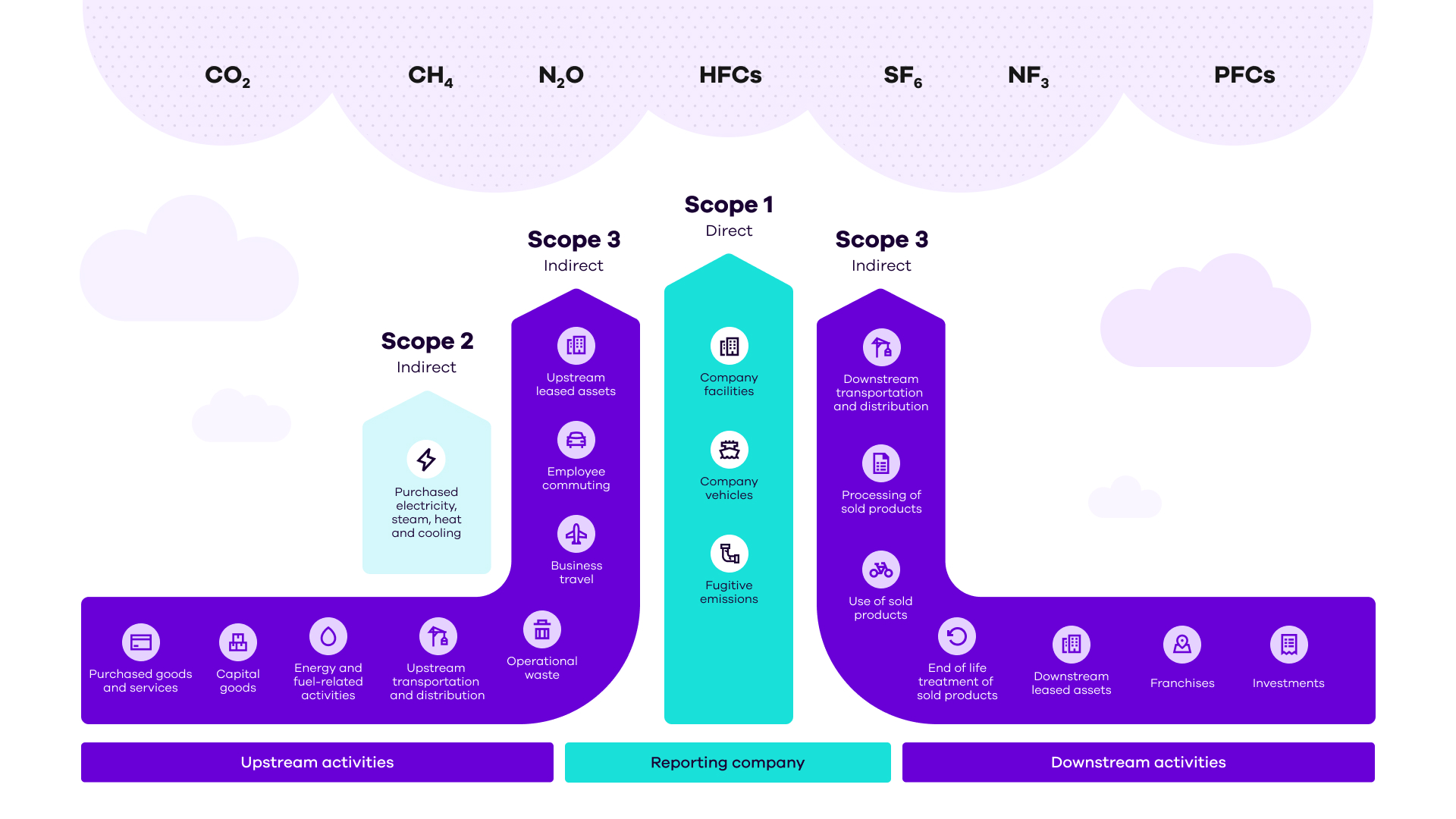
As a logistics manager, your main focus will be on collecting and reporting your company’s scope 3 emissions data.
Scope 3 emissions: A deep dive
Scope 3 emissions encompass all the emissions in your company’s value chain. By its very nature, scope 3 is broad, meaning it can be a challenge to grasp exactly what falls into this category for your business. However, it also accounts for 60% of all global emissions, meaning tackling them can have the biggest impact overall. To help quantify these emissions, the GHG Protocol breaks scope 3 down into 15 categories as part of its Scope 3 Calculation Guidance. These 15 categories are made up of activities that happen upstream and downstream of a business’s value chain.
Here’s an overview of the 15 scope 3 categories:
Upstream:
1: Purchased goods and services
2: Capital goods
3: Fuel and energy-related activities not included in Scope 1 or 2
4: Upstream transportation and distribution
5: Waste generated in operations
6: Business travel
7: Employee commuting
8: Upstream leased assets
Downstream:
9: Downstream transportation and distribution
10: Processing of sold products
11: Use of sold products
12: End-of-life treatment of sold products
13: Downstream leased assets
14: Franchises
15: Investments
As a logistics manager, the most important scope 3 categories you will need to focus on are categories 4 and 9 which deal with emissions from the transportation, storage and distribution of goods upstream and downstream of your business’s operations.
Scope 3 calculation methods in carbon accounting
Now you know what carbon accounting is and what emissions sources you need to consider, how do you actually measure your scope 3 emissions? Depending on the data available and the structure of your value chain, there are 3 primary methods for calculating scope 3 emissions: spend-based, activity-based and supplier-specific methods.
Spend-based calculation
This method uses the financial value of purchased goods or services and multiplies them by an emission factor which is essentially the amount of emissions per dollar spent. This method is straightforward but is considered relatively inaccurate because it relies on average data, which doesn’t account for the specific characteristics of each product.
Activity-based calculation
Instead of financial data, this method uses the physical quantity of materials (e.g., weight) multiplied by relevant emissions factors. While considered more accurate than the spend-based method, it also uses averages, which may not provide a high level of accuracy.
Supplier-specific calculation
This is the most accurate method, involving direct data from suppliers. This method involves collecting detailed information such as energy use or raw material sourcing from your suppliers so you can calculate emissions based on actual activities within your supply chain. This method provides the most precise insights but can be time-consuming and particularly complex due to a lack of transparency within global supply chains.
Hybrid approach
In practice, companies often start with spend-based calculations due to ease of implementation and then gradually move towards more accurate methods as they gather better data. Many companies rely on what is known as the hybrid approach which uses supplier-specific data where available and fills gaps with spend-based or activity-based estimates.
Section 2: Carbon accounting in your logistics supply chain
Carbon accounting specific to your logistics supply chain involves the calculation, management and reporting of carbon data from your business's indirect logistics activities. It’s a process that requires collaboration with your logistics partners such as freight forwarders who need to provide you with the emissions data from your shipments.
In this section, we break down logistics carbon accounting into 3 main steps to help you understand how it works and where to start.
Step 1: Calculating carbon emissions in your logistics supply chain
The first step involves converting shipment data into GHG emissions data. This phase is typically done by your logistics providers before they supply you with the finished calculation. However, it's important to understand how this process works so you can communicate clearly with your suppliers about your needs and expectations during the calculation phase.
Introducing the GLEC Framework
Transport and logistics already has an established methodology for calculating GHG emissions arising from freight activities. This methodology will guide you and your suppliers on how to measure and report your business’s scope 3 category 4 and 9 GHG emissions.
Created by the Smart Freight Centre (SFC), the Global Logistics Emissions Council (GLEC) Framework provides a comprehensive methodology for calculating the transport and distribution emissions from the upstream and downstream activities in a business’s value chain.
Significantly, the GLEC Framework is the only internationally recognised methodology for measuring and reporting carbon emissions from freight transport. It also provides the basis for the ISO 14083 standard for the quantification and reporting of greenhouse gas emissions arising from transport chain operations.
How does the GLEC Framework work?
The GLEC Framework offers differing levels of precision based on the detail of the data provided. At its most basic level, it uses only essential data to calculate an emissions estimate for a shipment. At its most precise level, it uses records from the actual vehicles used in transporting and distributing goods.
The GLEC Framework provides emissions estimates based on 3 main data input types:
Default data: These calculations are done using standard industry averages and assumptions — all of which can be found in the SFC’s End-to-End GHG Reporting Guidance — to estimate emissions from limited input data such as the cargo weight, distance travelled and emissions intensity factor. As this calculation type accounts for many unknown factors, the assumptions are typically conservative, usually resulting in an overestimation of the true emissions output.
Modelled data: While it’s possible to use default data to manually calculate carbon emissions, modelled data typically exists only within specialised carbon accounting software tools. It builds on default data and takes it further by incorporating more detailed vehicle and route-specific information. This could be vessel IMO numbers, carrier codes or flight numbers that enable you to use emissions factors for the exact vehicle type used, providing much greater accuracy. It can also incorporate factors like road type, route gradient or traffic conditions in road haulage.
Primary data: This is the gold standard for scope 3 carbon accounting in transport and logistics. It uses real records — usually in the form of fuel receipts or digital fuel consumption monitoring — from the vehicles used during the transport and distribution of your goods. While it generates the most accurate emissions calculations, it is often the least accessible for logistics managers due to the complex nature of their supply chains.
Understanding the different data input types is important. It enables you to gauge the quality of carbon emissions calculations you receive from your logistics providers and determine a minimum standard that you expect from them when you go out to tender.
Step 2: Supplier data collection and management in logistics carbon accounting
Accurately calculating the GHG emissions from your logistics supply chain requires comprehensive data management, especially as much of what you need will be sourced from your suppliers. This adds another layer of complexity to collecting and managing your scope 3 emissions data.
Challenges of logistics emissions data collection in carbon accounting
Differing levels of carbon reporting awareness: Not all logistics providers will have the same level of awareness or capability when it comes to calculating and reporting your shipment carbon emissions, leading to inconsistencies in data quality. Smaller suppliers, in particular, may lack the resources or expertise necessary to provide accurate emissions data.
Variability in reporting standards across different regions: With carbon reporting a relatively new concept, there are reporting inconsistencies across the different global regions. This can complicate the aggregation of your carbon emissions data into a consistent format for your records.
Varying data sources: When suppliers use different tools or methodologies to calculate and report shipment emissions, it can be difficult to make accurate comparisons and assessments of carbon emissions sources, ultimately leading to mismatched or fractured datasets.
Engaging with your suppliers during the carbon accounting process
To help overcome these challenges, engaging with your suppliers should be a fundamental part of your carbon accounting process. From the outset of any contract, make sure to clearly establish your expectations regarding scope 3 emissions reporting. This includes specifying the reporting standards they need to meet, the processes for submitting carbon reports, any deadlines and any contractual penalties for non-compliance.
Importantly, you should ensure they use a science-based approach — such as the GLEC Framework — for doing the calculations. This way, you can trust their calculations and have confidence when it comes to the reporting phase of the carbon accounting process.
To ensure new suppliers meet your carbon calculation and reporting conditions, thoroughly vet them on all of these aspects. Ask them about the methods and solutions they use to calculate and report GHG emissions and confirm that they can provide reports in the correct format for your records.
Just as financial due diligence is a necessary part of assessing new suppliers, carbon reporting due diligence should also be integrated into your procurement process. This ensures that your suppliers' carbon reporting capabilities will align with your sustainability goals.
Step 3: Carbon reporting in your logistics supply chain
Another key component of the carbon accounting process is proper carbon reporting. The GHG Protocol provides clear guidance on how businesses should report their emissions in their Corporate Accounting and Reporting Standard. The guidance specifies that your data needs to be accurate and well-documented to provide transparency, build stakeholder trust and meet mandatory climate disclosure regulations like the EU’s Corporate Sustainability Reporting Directive (CSRD).
Formatting carbon reports
Categorising emissions: Report emissions by scope and category, detailing the total emissions for each. This categorisation helps stakeholders understand the sources of your emissions and identify areas for potential reductions.
Justify exclusions: If there are any categories or activities that have been excluded from your report, you must provide a clear justification. This could be a lack of data or the insignificance of certain activities relating to emissions.
Clearly explain calculation methods: List and explain the calculation methods and data input types used to calculate emissions for each category. This transparency allows stakeholders to assess the credibility of your report and understand the basis of your emissions data.
Data quality and documentation
An important factor for good reporting is providing a clear indication of the data quality. This helps stakeholders identify how accurate and useful the carbon emissions calculations are for informing reduction strategies.
To do this, reports should include a data quality indicator (DQI), indicating the level of data quality in the reported emissions estimate at a more granular level. Providing a DQI as part of the reporting process is a element of meeting the ISO 14083 standard.
3rd party verification
Third-party verification is a critical step in the carbon reporting process. Verification by an independent assessor ensures that your report meets the required standards and is free from errors or biases. This process includes:
Compliance: Verification bodies assess whether your report complies with the GHG Protocol and other relevant guidelines. This step is particularly important for businesses subject to mandatory climate disclosures like the CSRD.
Credibility: Third-party verification enhances the credibility of your report, reassuring stakeholders that your emissions data is accurate and reliable.
Risk mitigation: Verification helps identify and correct any potential issues before your report is published, reducing the risk of fines or other penalties for non-compliance with regulations.
Reporting for climate disclosure regulations
With climate disclosure regulations already in force, businesses must be diligent in their carbon accounting practices — particularly the reporting phase. For example, the CSRD requires detailed and standardised climate disclosures, which include carbon emissions data across all 3 emissions scopes.
Additionally, non-compliance or improper reporting can result in significant fines as well as damage to your company’s reputation. To avoid these risks, you should ensure your reporting process aligns with any relevant climate disclosure regulations your business is subject to, paying close attention to data accuracy, correct formatting and verification requirements.
Section 3: Carbon accounting software tools
Carbon accounting can be daunting — especially if you’re under pressure to meet climate disclosure regulations or report to stakeholders. There are, however, specialised carbon accounting software solutions on the market that can help streamline the whole process. Carbon accounting software simplifies the complex tasks associated with carbon accounting at each stage of the process.
The benefits of carbon accounting software
Provide accredited carbon emissions calculations
Carbon accounting software can enable your logistics providers to convert raw shipment data into usable emissions estimates in line with industry-recognised methodologies like the GLEC Framework. When working with logistics providers, make sure to use GLEC-accredited solutions so you can have confidence in the estimates they’re providing.
Enhanced data collection
Once your suppliers have converted the shipment data into emissions data, carbon accounting software can facilitate the transfer of this data into your systems, significantly improving the efficiency and accuracy of your data collection processes. Instead of relying on manual, time-consuming email exchanges that lead to missed information or errors, your suppliers can directly upload their data into the system. Automating this process guarantees a reliable and comprehensive dataset.
Simplified scope 3 management and analysis
Carbon accounting software provides a comprehensive view of emissions across the entire supply chain, enabling logistics managers to identify trends, patterns and key areas for improvement using a series of dashboards and analysis tools. Features like the DQI ensure that all collected data is standardised and comparable. You can use these special features to highlight emissions hotspots within your supply chain, offering actionable insights that can help inform decision-making and allow you to be more strategic in your approach to setting carbon reductions.
Streamlined emissions reporting
At the other end of the carbon accounting process, carbon accounting software can be used to streamline your reporting capabilities. It allows you to quickly generate reports that are formatted to meet the reporting standards required for climate disclosure regulations or your own ESG reporting needs. These software solutions can streamline report sharing, helping to reduce the time spent on administrative tasks and eliminate reporting errors.
To find out more about carbon accounting software, read our blog: How carbon accounting software can transform logistics management.
Section 4: How logistics managers can get started with carbon accounting
Reading this blog post means you’ve already taken the first step to getting your carbon accounting journey up and running. Here’s what you can do to lay the foundations for effective carbon accounting practices at your business:
1. Build your knowledge
The first step in carbon accounting is understanding the fundamentals. This involves getting familiar with how carbon accounting works and identifying your business's specific requirements. While this blog covers the basics, it's important to dive deeper into the key topics to ensure a thorough understanding. Here’s a list of key resource centres for building your carbon accounting knowledge:
2. Explore carbon accounting software tools
Once you have a good grasp of the basics, start exploring different carbon accounting software tools. There are many options on the market, ranging from tools designed specifically for supply chain logistics to more general solutions. It’s crucial to take the time to compare these tools and evaluate them against your business's unique needs. When it comes to carbon accounting specifically for your logistics supply chain, you’ll want to ensure you choose a tool that’s GLEC-accredited and ISO 14083-aligned.
3. Engage your suppliers
Involve your suppliers in your carbon accounting efforts from the get-go. Many freight forwarders and logistics service providers aren’t even aware that their shippers will need to start managing and reporting their carbon emissions. By notifying your current logistics providers about your plans and outlining how they need to support you, you can ensure a smoother transition and get them onboard. You should also make carbon reporting a key part of your procurement process for when you go out to tender. This will ensure that any new suppliers you onboard also adhere to your new carbon reporting requirements.
4. Refine your processes
Once you have built your knowledge, chosen a carbon accounting software tool and engaged your suppliers, you’ll want to set a review process that allows you to learn, analyse and refine your current carbon accounting procedures. This might mean providing suppliers with incentives to improve the DQI scores on their emissions estimates, or exploring ways of providing additional transparency to customers and stakeholders using dashboards.
What next once you've established a carbon accounting process?
Carbon accounting is only the first step in the process of decarbonising your business’s operations, but it’s a crucial step that every business will need to start with.
Once you have established and refined your carbon accounting process, you’ll be well-positioned to identify emissions hotspots where reductions can be achieved in your business’s logistics supply chain.
Keep an eye out for our next long read all about how you can engage with your logistics providers to actively reduce your business’s scope 3 emissions.